
Problems
- Low equipment utilization on the production line, aiming to increase machine utilization and personnel efficiency.
- Various types of customized products make scheduling difficult, leading to challenges in managing order lead times.
- Paper-based forms result in the inability to output production data in real-time.
- High levels of semi-finished inventory requiring inventory control.
- Analysis needed to identify abnormal productivity among personnel.
- Discrepancies between production hours and scheduling need analysis.
- Statistical analysis of downtime and idle time between each process.
Solutions
- Tablet-based Reporting App System
- Collects production data (work orders/quantities/production hours/production frequency/downtime/downtime reasons).
- Analyzes machine/personnel efficiency (individual data analysis by product type/machine type/process type/operator).
- Mutual verification of personnel assigned tasks by production management; if personnel reporting exceeds the set allowable value, a red light will flash.
- Any downtime requires employees to press “stop” on the tablet reporting app system, followed by selecting the downtime reason, including mold change, parts shortage, upstream failure, conveyor belt failure, etc., with a customized list of options, providing immediate machine failure analysis after the work order is completed.
Advanced Production Scheduling (APS) System for Flexible Dynamic Production Planning to accommodate rush orders and address small-batch, diverse orders. Utilizes production progress boards to compare production progress with scheduling to identify progress or delays (indicated by warning lights).
Strengthened in-process management (traceability) to enhance transparency of production information and address high semi-finished inventory issues.
Establishment of SOPs including standard production hours and machine standard capacity. Reports discrepancies between actual production hours and machine output as a reference for personnel and machine improvements.
Real-time visualization interface to view data records instantly and export for further analysis.
Integration with the company’s cloud, ERP, and MRP systems.
Targets
- Small to medium-sized metalworking industries.
- Factories undergoing IT/OT/DT integration towards smart factory upgrades.
Software Specifications
- Scope of digital system implementation and integration with overall digital information: Imports data from ERP system BOM files, procurement files, order files, inventory files, and work order files.
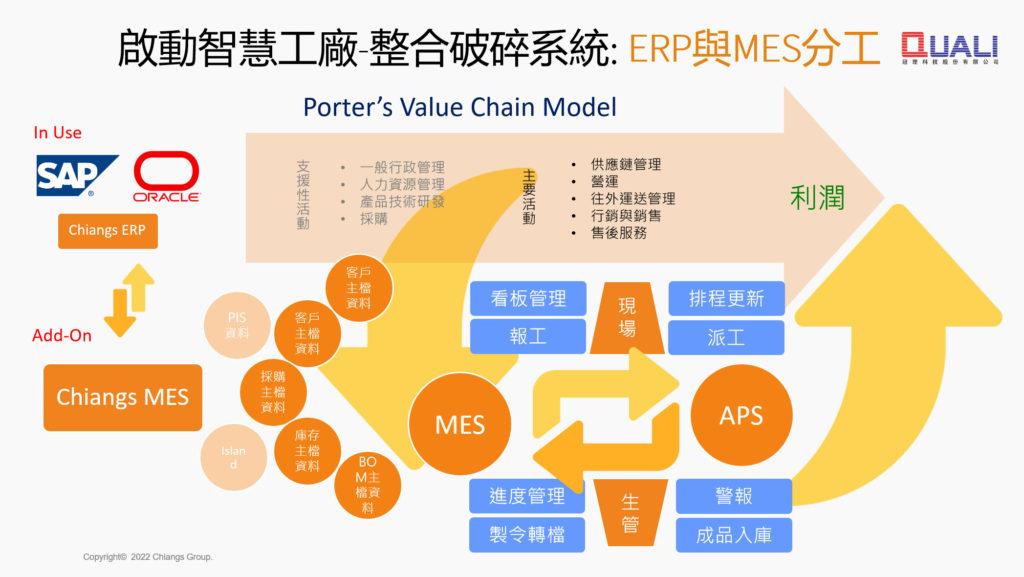
2. Advanced Production Scheduling (APS) functionality includes:
- Total planning staff runs the MPS (Master Production Schedule) main production plan, and after rough capacity balancing, tasks that can be arranged are set to a locked state to prevent confirmed plans from being modified.
- APS module reads the locked tasks from the main production plan.
- Expands the product BOM structure to APS and performs production task sorting to determine the priority sequence.
- Sets the priority sequence and traverses the task queue from high to low priority.
- According to capacity definitions and calculations, each task is assigned to individual machines and mold resources.
- If no machines are available for the day, the tasks are postponed to the next day, and so on until all tasks in the queue are scheduled.
- If some tasks are scheduled after the delivery date of the order, the system automatically notifies the sales company to renegotiate the delivery date with the customer, and schedules based on the newly confirmed delivery date.
- Tablet Reporting App inputs the work status and the quantity of good and defective products. Production management (PC) binds personnel, work orders, equipment, and raw materials together based on capacity. When starting and finishing work, the tablet app records equipment and personnel utilization rates, product output quantities, and performance. The tablet reporting app can view product design drawings, check quality history, and inquire about material shortages. The related functions are as follows:

- The Production Progress Dashboard is a real-time monitoring platform based on tablet computer apps, integrating mathematical algorithmic analysis techniques. It effectively and quickly grasps the production progress indicators of each work section. The Production Progress Dashboard efficiently supervises the production process, quality control, and packaging processes by embedding the Advanced Production Scheduling (APS) module. Any abnormalities in the production process are immediately highlighted on the dashboard, reducing the time required for abnormal handling and tracking order progress.
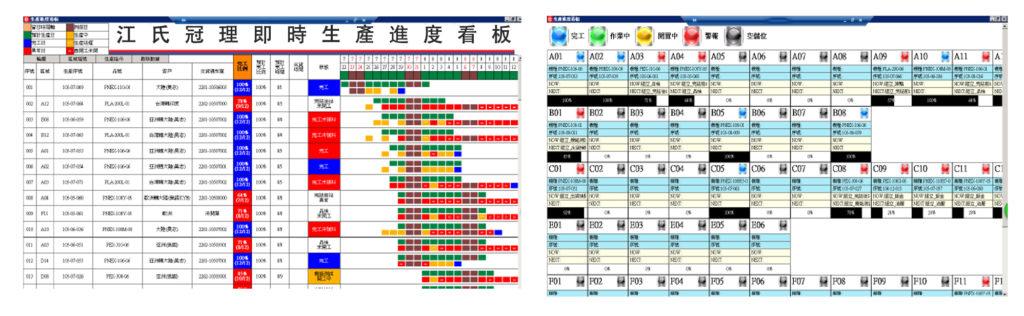
5. When the defect rate exceeds the Key Performance Indicator (KPI) in any manufacturing process segment, anomalies are promptly displayed and an email notification is sent to the quality control department. This helps reduce the quantity of defective products and minimize losses.