
傳統痛點
1) 生產線稼動率不彰,希望能提升機台稼動率與人員效率
2) 客製品種類繁多、排程不易,訂單交期難掌握
3) 紙本填寫表單,生產數據無法即時輸出
4) 半成品庫存偏高希望能控管存貨
5) 希望分析人員生產效率是否出現異常
6) 生產工時與排程差異分析
7) 停機時間做統計分析、每一製程間停滯浪費時間分析
解決方案效果
1) 平板報工APP系統
1.可蒐集生產數據(製令/數量/生產工時/生產頻率/停機時間/停機原因)
2.分析機台/人員效率(可依產品別/機台別(製程別)/作業者做個別數據分析)
3.和生管預定的人員指派工作互相稽核,人員報工產量有異常於設定容許值,逾越容許值將閃爍紅燈。
4.任何停機時員工必須在平板報工APP系統上按下中止,進一步按下停機故障的選項,包括換模、缺件、前站故障、傳送帶故障、……等客製化品項,在製令結束後立即提供機台故障分析表。
2) APS先進生產排程系統可彈性動態調整生產計劃 急單、因應少量多樣化的訂單
並利用生產進度看板比對生產進度與排程,是否有依進度或延遲(燈號訊息示)。
3) 加強在製品管理(履歷追溯),透明化生產資訊,改善半成品庫存偏高問題。
4) 建立SOP包括生產標準工時、機台標準產能,將會與實際生產工時和機台產量列出差異報告,作為人、機改善的參考。
5) 即時可視化畫面,即時查看數據記錄、也可匯出進行後段分析
6) 可與公司的雲端、ERP、MRP系統整合
適合對象
1) 中小型金屬加工產業
2) 工廠進行IT/OT/DT整合,朝向智慧工廠升級
軟體規格
1) 數位化系統導入範圍與數位資訊整體串接應用作法:
透過ERP系統之BOM檔、採購檔、訂單檔案、庫存檔案、製令檔案進行匯入作業
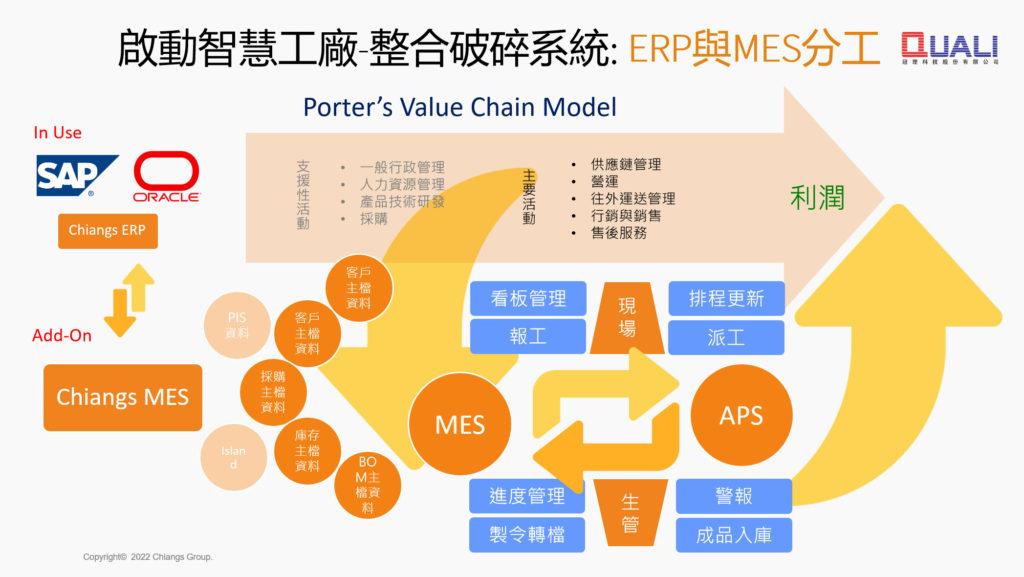
2) APS先進製造排程功能如下:
a. 總計劃員運行MPS主生產計劃,經粗能力平衡後,將可以安排的任務設置為鎖定狀態,以防止確認的計劃被修改;
b .APS模組讀入主生產計劃已經鎖定的任務;
c.按產品BOM結構展開到APS,進行生產任務排序,確定優先順序;
d.將設定好的優先順序,按由高到低的順序遍歷任務隊列;
e.根據產能定義和計算,將每一任務按機台與模具資源分配到單個機臺上;
f.如果當天沒有可用機台,就順延到下一天,以此類推直到隊列中的任務全部被安排;
g.如有些任務被安排到訂單的交貨期之後,系統自動通知銷售公司,使其與客戶重新協商訂單的交貨日期,並根據重新確定的交貨日期進行排程。
3) 平板報工APP輸入報工狀況及產品良品及不良品數,生管(PC)依據產能把人員、製令、設備和原料綁在一起。當起工和完工時平板電腦APP記錄設備和人員稼動率、產品產出數量與績效。平板報工APP可看產品設計圖檔、查詢品質履歷、查詢欠料狀況,相關功能如下

4) 生產進度看板即時監控平臺以平板電腦App為基礎、導入數學演算分析技術,有效快速掌握各工段訂單生產進度指標,由生產進度看板有效快速監督製程生產流程、品管及包裝等各工段嵌入先進製造排程(APS)模組,在製流程有異常看板馬上顯示亮燈,可減少異常處理時間與追蹤訂單流程進度
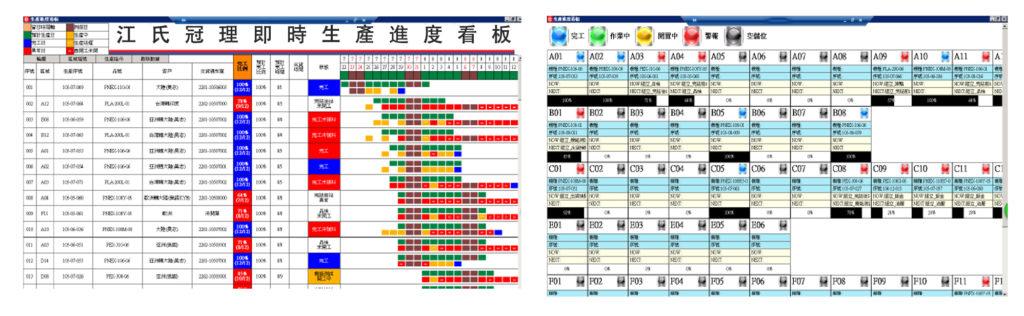
5) 在製造流程工段不良率超過KPI時即時顯示異常並且email通知品管部門,可降低瑕疵品數量以減少損失。