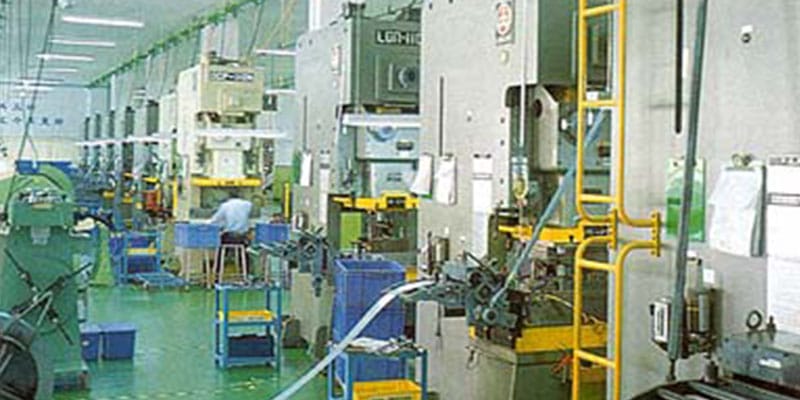
ARENA Metal:specializing in large stamping presses, with a staff of 200-300 employees, located in Dongguan.
1.Control Focus:
Engineering Department: Establishing hierarchical BOM and process management. Each model consists of over 600 parts and components, with each part having semi-finished products and sub-parts. Semi-finished products require raw material procurement and multiple processing steps, including some outsourced processes and some in-house processing. These processes are interlinked, and the entire machinery’s hierarchical structure and total cost rely on BOM and process operations.
Production Management Department: Focuses on order production. Upon receiving orders, the Jiang software’s SO2MO (Sales Order to Manufacturing Order) is used to convert orders into multiple production orders based on the parent and child BOM. Semi-finished products requiring processing are then batch-converted into manufacturing orders using MO2PD (Manufacturing Order to Production Order).
Purchasing Department: Utilizes MO2PO (Batch Material Demand) to convert material requirements into purchase orders. The first screen aggregates similar materials into a material demand table. The second screen compares inventory levels, planned production quantities, and safety stock to generate a shortage list. The third screen compares prices from multiple suppliers and defaults to the lowest price, but manual selection of other suppliers is possible. The fourth screen previews the purchase recommendation, and the purchase order is submitted after confirmation.
Warehouse QC Department: Upon receipt, suppliers’ shipments are placed in the awaiting inspection warehouse, undergo IQC (Incoming Quality Control) inspection, and are judged based on AQL standards for acceptance, rejection, or special acceptance for inventory. Quality Pareto charts, as well as supplier defect rates and delayed delivery rates, can be generated.
Warehouse Department: Prints barcode-equipped material requisition forms for material retrieval from the warehouse. Warehouse personnel scan the barcode on the requisition form, update the inventory, allocate the materials to the designated location, and deliver them to the manufacturing department either manually or using carts or cranes for large items.
Manufacturing Department: Each process order is equipped with a barcode. Upon initiation and completion of each process, the barcode is scanned to record actual working hours for each process and to automatically generate daily production reports.
Outsourced Processing: Barcode scanning is used to record the initiation and completion of processing tasks. The system automatically calculates subcontracting costs and accounts payable based on these records, without considering working hours.
2.Benefits:
Enhanced Visibility: Transitioning from manual Excel-based accounting to using the BOM (Bill of Materials) structure has provided comprehensive insight into the entire machinery framework. This allows for real-time monitoring of the cost structure associated with production and materials.
Time Savings in Procurement: The adoption of MRP (Material Requirements Planning) functionality for procurement has significantly reduced the time required for material calculation, lead time estimation, and price comparison. What previously took a week can now be accomplished in just five minutes, ensuring no small parts are overlooked in procurement.
Improved Production Monitoring: The use of the Jiang software enables monitoring of production line progress and outsourced processes without the need to physically enter the workshop, enhancing overall production control.
Efficiency in Reporting: Daily production reporting, previously done manually, has been streamlined with barcode scanning replacing manual data entry. This has saved considerable time and reduced repetitive tasks.
Enhanced Performance Evaluation: Barcode implementation in the workshop has provided more reliable tracking of work hours, facilitating fair performance assessment and enabling the implementation of performance-based incentive schemes.
Cost-Effective Management: Barcode-based management promotes self-discipline among employees, reducing the need for intensive supervision and warning employees of potential delays, thus enhancing overall management efficiency.
User-Friendly Operation: The simplicity of operating the Jiang software, requiring only basic training to use barcode scanners, has led to high acceptance among production line workers. Printing manufacturing orders with laser or inkjet printers is straightforward, and the overall system can be quickly implemented, typically within two months.
Time and Error Reduction in Inventory Management: Barcode-based material requisition and storage processes have reduced data input time and minimized errors, leading to increased inventory accuracy and reduced time spent on error correction.